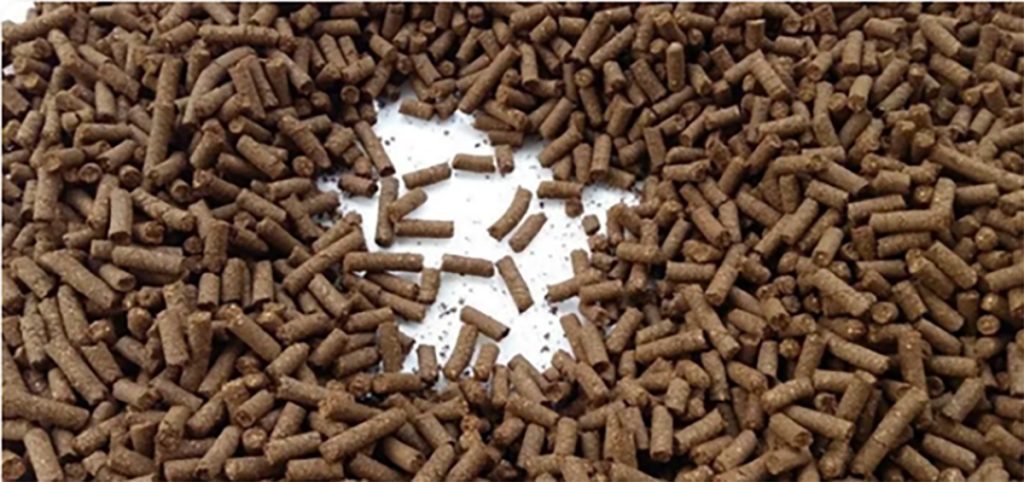
- The pellets are curved and have many cracks on one side
This phenomenon usually occurs when the particles leave the ring die. When the position of the cutter is adjusted far away from the surface of the ring die and the knife edge is blunt, the particles are broken or torn by the cutter when they are extruded from the die hole. When cut, some pellets are bent to one side and many cracks appear on the other side.
Improvement method:
- Increase the compression force of the ring die on the feed, that is, increase the compression ratio of the ring die, thereby increasing the density and hardness of the pellets;
- Crush the feed ingredients more finely. If molasses or fat is added, the distribution uniformity of molasses or fat should be improved and the amount added should be controlled to increase the density of the pellets and prevent the feed from becoming soft;
- Adjust the distance between the cutter and the ring die surface or replace it with a sharper cutting blade;
- Use adhesive granulation additives to improve the binding force inside the particles.
2. Horizontal cracks across the entire pellet
Somewhat similar to the phenomenon in case 1, cracks occur in the cross-section of the particles, except that the particles are not bent. This can occur when fluffy feeds containing high amounts of fiber are pelleted. Because it contains fibers that are longer than the pore diameter, when the pellets are extruded, the expansion of the fibers causes transverse cracks in the cross section of the pellets, resulting in a fir bark-like feed appearance.
Improvement method:
- Increase the compression force of the ring die on the feed, that is, increase the compression ratio of the ring die;
- Control the crushing fineness of the fiber, and its maximum length cannot exceed one-third of the particle diameter;
- Reduce the output to reduce the speed of feed passing through the die hole and increase the density;
- Extend the conditioning time and use a multi-layer conditioner or kettle-type conditioner;
- When the moisture content of the powder is too high or contains urea, it may also produce a fir bark-like feed appearance. The added moisture and urea content should be controlled.
3. Improvement method:
The feed formula contains fluffy and slightly elastic raw materials. When they are conditioned by the conditioner, they will absorb water and expand. After being compressed and granulated by the ring die, they will pop open due to the action of water and the elasticity of the raw materials themselves, resulting in Vertical cracks.
Ways to improve:
- Adding adhesive helps reduce the occurrence of vertical cracks;
- Use relatively saturated dry steam;
- Reduce the output or increase the effective length of the die hole to increase the residence time of the feed in the die hole as much as possible;
- Change the formula, but doing so may increase the cost of raw materials;
4. Radial cracks occur in granular materials from a source point
This appearance indicates that the pellet material contains large particle raw materials. It is difficult for these large particle raw materials to fully absorb the moisture and heat in the water vapor during conditioning. They are not as easy to soften as other finer raw materials. At this time, due to the different degrees of softening, the amount of shrinkage is different, resulting in radial cracks and an increase in the powdering rate.