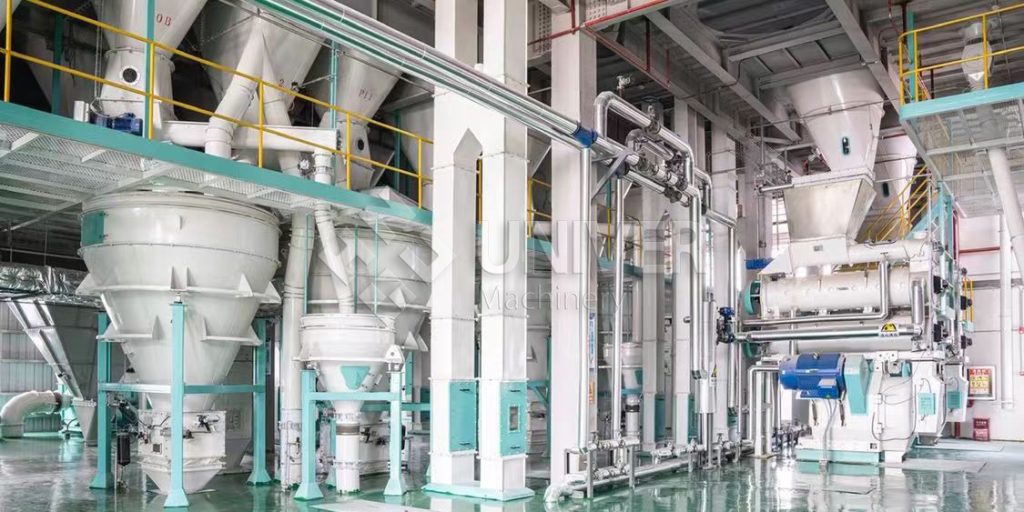
The feed formula determines the production process, which is mainly reflected in:
1. Determine the processing technology of raw materials
For example: when producing puffed suckling pig feed, puffed corn is used, but the processing techniques are different. One method is to puff the corn, then mix it with other raw materials, and then pellet it; the other method is to first mix the corn with other raw materials and then puff it. The suckling pig feed produced by these two processes can both be called extruded feed, but the processes are different.
2. Determine the shape of the finished feed product
In the early stages of the development of the feed industry, feed products only came in the form of powder. However, with the emergence of advanced processing technologies such as pelleting technology, puffing technology, post-curing technology, and post-spraying technology, the appearance of feed has become more colorful. Products can be produced in different shapes according to different formulas.
3. Determine the crushing particle size of raw materials
The grinding process is the basic operating unit of feed processing and an important process in the feed processing and production process. The grinding operation involves feed processing costs (power consumption, vulnerable parts), raw material loss (moisture and dust), mixing uniformity, and pellet feed quality. Waiting steps. The crushing particle size of raw materials varies according to the requirements of the formula. Generally speaking, the requirements for the crushing particle size of the formula are mostly marked in mesh. However, in actual production, the aperture of the crusher is mostly calculated in millimeters. Therefore, unit conversion must be performed during application, and the crushing particle size must be tested to determine the optimal Optimal production process parameters.
4. Determine the process parameters of the granulation system
For different products, the process parameters of the granulation system will be different. Even for similar products, process parameters such as conditioning time, ring die aperture, ring die compression ratio, cooling time, classification screen aperture, etc. will also occur due to different formulas. Variety. For example, the ring die compression ratio of ordinary aquatic products is generally 13-16. Such a design is beneficial to reducing the powdering rate and powder content of the product, and can also meet the stability of the product in water. However, through the selection of raw material varieties and raw materials After the proportion adjustment, after meeting the same requirements, the ring die compression ratio can be reduced to 8, and the production efficiency is significantly improved.